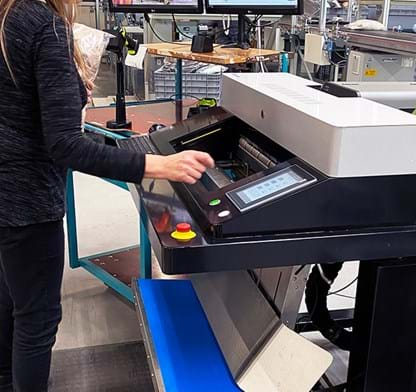
Customer case Wehkamp & Speedpack Hybrid
Speedpack plays an import role in Wehkamp's fast, efficient and reliable delivery of products.
Choose a country to view content specific to your geographical location
Product case
A well-established automotive multinational has ap-proached Audion for designing a packaging solution to pack a wide variation of automotive spare parts of various dimensions and weights.
A well-established automotive multinational has approached Audion for designing a packaging solution to pack a wide variation of automotive spare parts of various dimensions and weights.
In this warehouse, being the central European distribution center for automotive parts of a well-known car brand in Germany, 30.000 different parts need to be packed in different bag widths and bag lengths. Total packaging volume per week: 210.000 bags. Due to the wide variation in parts and bag sizes all the warehouse packaging of spare parts used to be done manually, effecting in a packaging output of 2 bags per minute per person. Packaging costs of parts preparation at this big automo-tive company were huge. They needed more than 40 employees per day for packing the 40.000 bags.
Efficiency challenge:
Due to the wide variation in spare parts the packaging costs were extremely high. This warehouse had to cope with high labour costs (> 40 fte), high costs of packaging material and high storage costs (due to the various bag sizes they had to stock). Also, handling costs were high as every new batch of spare parts needed a new supply of bags (many logistic movements).
The packaging output per minute had to increase from 2 bags per minute to a minimum of 15 bags per minute (7.200 bags per day per machine). Total required pack-aging output per day: 40.000 bags per day.
Technical challenge:
The wide variation in part sizes demands a highly flexible packaging system in which bag sizes can easily be changed. Also, due to the wide variation in weight and size among the parts, some bags need extra bag support for packaging and cannot be packed by automatic infeed.
Product packaging specifications:
Weight variation per part: 1 gram – 3.000 gram
Current bag dimensions: 80 x 80 mm, 100 x 800 mm,
400 x 400 mm
Film thickness: 60 micron
Audion had to design a packaging solution offering the widest possible flexibility for packaging and labelling the many different automotive parts at one machine at maximum efficiency. Following the lean manufacturing strategy this well-established automotive multinational has implemented, our packaging solution should guarantee full flexibility and guarantee the highest reliabi-lity.
By implementing automation of parts packaging, this warehouse should be able to increase the packaging output per employee. Also, they would save a huge space in the warehouse as all parts were packed at various packaging tables, each manned by two employees.
Audion constructed the Speedpack Hybrid High Speed for realizing maximum increase of their packaging out-put from 2 bags per minute up till now 30 bags per minute. Due to the patented bag making assembly of Speedpack Hybrid High Speed, bags can easily be crea-ted at the desired length, at high speed. Above all, each bag will be labelled with product description, barcode etc.
Audion investigated all the spare parts to be packed and labelled (more than 30.000 different parts!) and we categorized them in 4 types of packaging:
Packaging of small parts in small bags
(80 or 120 mm wide bags)
manual bag filling at Speedpack, fast bag creation and bag opening, using special fixed hopper for easy filling, photocell start for automatic start of packaging cycle during manual filling.
Packaging of big parts in wider bags
(280 mm)
manual bag filling at Speedpack, fast bag creation and bag opening, using special fixed hopper for easy filling, bag open and bag detection system, photocell start for automatic start of packaging cycle during manual filling.
Packaging of big and heavy parts in wide bags
(280 mm)
manual bag filling at Speedpack, fast bag creation and bag opening, using special fixed hopper for easy filling, bag open and bag detection system, photocell start for automatic start of packaging cycle during manual filling, discharge conveyor, to support and feed out the heavy products.
Automatic packaging of small bulk parts
2 parts per bag (80 mm)
Automatic infeed by Optimizer including sorting table.
Optimizer with sorting table generates fast preparation of subassemblies and kits of spare parts.
The sorting table has been adapted for the operator, enabling the operator to stand behind the sorting table, shifting the parts onto the conveyor.
Finally, we integrated an emergency button on the sorting table for quick stop of the system.
Technical configuration of Speedpack Hybrid:
As basis this packaging solution is composed by the Speedpack Bags on roll version (400 SPKR – CONF) to-gether with the High Speed Assembly including the bag-open-assembly ( 400 SPKR HS), enabling to create batches of bags at variable bag lengths at high speed.
From the touchscreen easy change of product batches can be set. All product recipes can be stored guaran-teeing a reliable quality package, being independent of operator.
Extra product solutions mounted for this project:
- Special working height 775
(for connecting to Optimizer)
- Extra funnels (accumulating funnels and
fixed funnels of various sizes for quick exchange)
- Optimizer incl. sorting table
- Easy bag open and bag detection system
- Film End detection
- Discharge conveyor
- Photocell start for manual filling
- Additional film reel (for quick exchange of film rolls)
- Thermal label printer
Increase of output per employee
This central European distribution warehouse for auto-motive spare parts is massively impressed by the increase of output per packing employee realized by integrating Speedpack Hybrid High Speed into their packaging processes. The 40.000 bags per day used to be packed by more than 40 employees.
Now, by implementing the Speedpack Hybrid High Speed this packaging output is realized by 7 Speedpack Hybrid High Speed machines, operated by 10 -14 employees (1 fte for operating each Speedpack, 0,7 fte for product supply to each packing station: supply of spare parts to be packed and film rolls). Output per employee has increased by 250%.
Gain of work space
Further, since the integration of Speedpack Hybrid High Speed, the footprint required for packaging the 40.000 parts is restricted to the space required for 7 units Speedpack packaging machines, some including the Optimizer, compared to the former 15 pack stations operated by 40 employees. An amazing gain of work space has been realized.
Reduction of material handling
The diversity in bags has been reduced from 20 bag sizes to 3 sizes of LDPE lay flat tubing. This considerably reduces the number of logistic handlings from storage to the packing stations.
Reduction of material storage
Due to the fact that ready bags do not need to be stocked anymore, less space is needed for stocking packaging material. From the lay flat tubing bags in different lengths can be created and the film rolls take up considerably less space than stocking all the cartons with ready bags.
Reduction of packaging material
Less LDPE film is used to pack the products as every product batch can be packed at the right size, not wasting film anymore.
International Sales
Audion
Would you like to know more about this case or how we can help you optimize your packaging process? Get in touch!