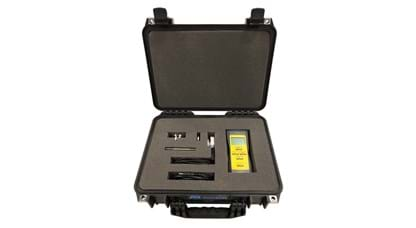
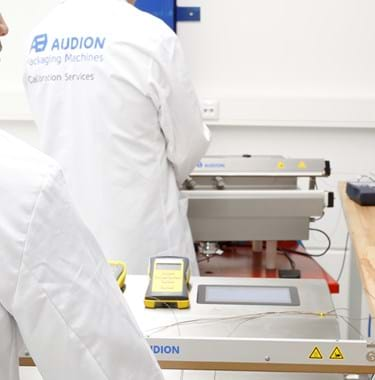
Audion services
Calibration, Verification and Validation Services
Audion's calibration and verification services ensure optimal seal integrity in compliance with the latest industry standards.
Interested in our Calibration or IQ/OQ Services?
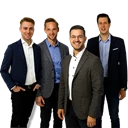
We are more than willing to support you with your request.
Audion Calibration, Verification and Validation Services
Audion offers comprehensive calibration services for our extensive range of validatable sealers, widely used in the Medical, Pharma, and high-tech industries. All our validatable sealers, validatable continuous bandsealers, validatable Speedpack and validatable vacuum chambers can benefit from our services. Regular user verification and annual re-calibration ensure that our sealers consistently deliver the required seal quality.
The quality and consistency of the seal are determined by three key parameters: temperature, time/speed and pressure/force. For vacuum chambers, vacuum pressure is also a critical factor.
During calibration, our service engineers meticulously calibrate and adjust these parameters as needed, providing you a traceable calibration certificate issued in accordance with an ISO 9001 quality management system.
Our reference standards are calibrated under ISO 17025 accreditation, ensuring traceability to national and international standards.
We offer three distinct services for the calibration and validation of our packaging machines:
- Audion Factory Calibration
- IQ/OQ Check (Installation/Operational Qualification)
- Seal Integrity Tests
Audion Factory Calibration ensures precise sealing parameters of the packaging machine, marking the first step towards ISO 11607-2:2019 compliance.
The subsequent IQ/OQ Check verifies that the machine and materials consistently produce the required seal. Audion provides essential documentation for your validation process.
We also provide Seal Integrity Tests as a standalone service. Our technician will use calibrated instruments and test kits to conduct thorough inspections. A detailed certificate, including all relevant documentation, will be provided upon completion. For regular seal inspection, we offer a comprehensive range of tools and accessories tailored to your specific needs.
Ensuring Sterile Packaging
Medical packaging is regulated as stringently as medical instruments worldwide, emphasizing its crucial role in patient care. This emphasizes the importance of reliable packaging, enabled by Audion’s validatable packaging machines.
Validatable Sealers and Compliance
Audion Packaging Machines provides companies active in the Medical/Pharma market not only with reliable validatable sealers but also with calibration and validation services to ensure that your packaging always complies with the strict requirements of ISO 11607-2:2019. Our services are essential because traceability, reproducibility, and the availability of documentation are central to the standard and depend on regular verification, calibration, and validation.
Calibration and Validation Services
Audion offers its customers all the necessary calibration and validation services as well as a range of tools for regular verification, allowing customers to independently monitor and maintain their seal quality. By combining these services and tools, Audion ensures that customers can maintain the highest standards of packaging quality and compliance, providing confidence in the sterility and safety of their medical devices.
Importance of IQ/OQ Check
Our IQ/OQ Check ensures that the packaging machine and the material together provide the required result: the right, consistent seal. The documents Audion provides after completing both stages will be a significant part of your validation process.
Seal Integrity Tests and Additional Services
We also provide Seal Integrity Tests as a standalone service. Our service engineer will visit your facility equipped with calibrated measuring instruments and test kits. Upon completion, we will issue a certificate along with all relevant documentation.
Re-calibration: As-found
Audion’s re-calibration services ensure the accuracy of critical process parameters after a year of use, often serving as the final step to clear your annual production. The subsequent pre-check, maintenance, and as-left calibration ensure that your validatable sealer is ready for daily production. Our Service Team will provide all necessary documentation. We recommend annual re-calibration for packaging machines used to seal products subject to strict requirements.
As-found Calibration
As-found calibration is essential for demanding markets. Quality control processes, industry standards, certifications, or regulations often require regular re-calibration of packaging equipment. During as-found calibration, all applicable parameters—temperature, time, force, and, in the case of a vacuum chamber, vacuum pressure—are measured three times.
As-found Verification
For many customers, the cost-effective ‘As-found verification’ option is a valuable check to verify if their production run has been packaged as required. Our specialist performs single checks of the essential temperature and force parameters, as well as an initial inspection to ensure the device is functioning properly. While less thorough than as-found calibration, it effectively covers the necessary ground to clear production, especially when combined with regular user verification.
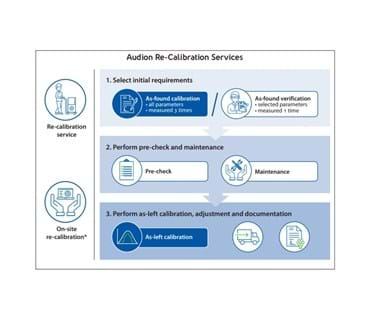
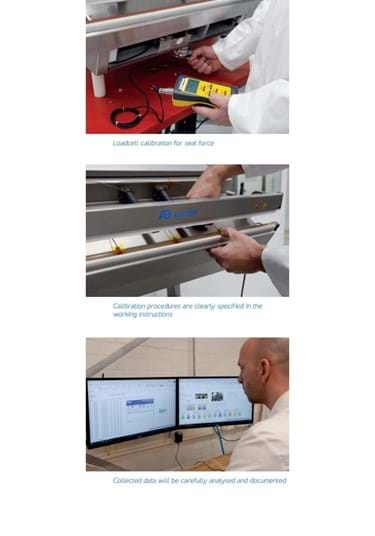
Re-calibration services: Maintenance / As-left / On-site
Maintenance
Maintenance is conducted through a comprehensive inspection where our engineers perform the following checks:
- Test wear-sensitive parts
- Verify seal regulation on operation and set parameters
- Conduct internal and external visual inspections of the machine
- Ensure the correct functioning of electrical and pneumatic components
- Review application settings
As-left Calibration:
Our service engineers perform as-left calibration to match the original factory standards. When necessary, we adjust parameters to ensure that your seal temperature, force, duration, and vacuum fall within the predetermined values. Calibration results are documented in accordance with ISO 9001 standards.
On-site Calibration Option:
We offer re-calibration services for Audion sealers both at our Calibration facilities and, for selected packaging machines, on-site. Our representative will inform you of your options during machine selection or when re-calibration is required
Audion Verification Instruments
Available Audion Verification Instruments
Regular verification of operational parameters, integrated with routine maintenance, is essential to proactively identify and address potential performance issues. Audion's comprehensive range of verification instruments empowers customers to conduct regular checks on seal parameters, ensuring early detection of any inconsistencies.
- Audion Temperature Meter (ATM)
- Suitable for: Validatable PSR, PSR TC, PSR PLUS (IP65), MSIDV, Validatable Contimed, Validatable Audionvac, Speedpack Hybrid (SPKH)
- Audion Seal Force Measurement Ring (AFMR)
- Suitable for: Power Sealer (VAL PSR, PSR PLUS (IP65), Validatable Bandsealers and Medseal® (MSIDV)
- Audion Seal Pressure Meter (ASPM)
- Suitable for: Validatable Audionvac vacuum chambers (VAL VMS)
- Audion Vacuum Pressure Meter (AVLM)
- Suitable for: Validatable Audionvac vacuum chambers (VAL VMS)
- Audion Peel tester (APT 100)
- The Audion APT 100 peel tester is ideal for verifying the tensile strength of seals on a wide range of packaging materials, especially those used in life-science and food applications.
IQ/OQ: Ensuring Packaging Machine Performance
Maintaining consistent and reliable packaging is crucial, especially when it comes to validatable (medical) devices. Audion offers a comprehensive solution to ensure your packaging machines operate at peak performance and comply with ISO 11607-2 standards. This includes essential Installation Qualification (IQ) and Operational Qualification (OQ) checks, conducted by our experienced service engineers at your location.
Installation Qualification (IQ): Verifying Proper Setup
This process guarantees your packaging machine is installed and configured according to Audion's specifications and installation checklist. Our engineer inspects for correct installation and functionality. All critical parameters and documents are reviewed for completeness. Comprehensive training is provided to your staff on operation and maintenance.
Operational Qualification (OQ): Optimizing Performance
The OQ phase focuses on determining the optimal parameter settings and tolerances for your specific packaging needs. This includes establishing acceptable criteria for consistent closure quality. "Worst-case testing" pushes parameters to their upper and lower limits, followed by integrity tests on these samples. These integrity tests include seal checks (EN ISO 11607-2), dye penetration tests (ASTM F 1929), and peel tests (EN 868-5:2018 Annex D).
IQ/OQ Documentation: Maintaining Compliance
Audion provides all necessary documentation for IQ and OQ, facilitating validation of your packaging machines. Developed in accordance with ISO/TS 16775:2014 checklists, these documents become crucial components of your overall validation record. The documentation will be delivered to you digitally for easy access and record-keeping.
Investing in Peace of Mind
By choosing Audion for IQ and OQ checks, you gain peace of mind knowing your packaging machines are operating optimally and are compliant with ISO 11607-2 standards. This translates to consistent, high-quality packaging, ultimately contributing to the safety and integrity of your validatable (medical) devices.

Seal Integrity Tests
Regular verification of your packaging seal quality is critical for maintaining product integrity and preventing contamination. Audion offers a comprehensive Seal Integrity Test service to support your quality control efforts. Our experienced service engineer visits your facility with specialized testing kits to perform a series of in-depth assessments.
Seal Check ( ISO 11607-2) and Peel Test (EN 868-5 Annex D)
These sections make sure the seal is intact for a specified seal width and the tensile strength of the seal, which is a key indicator of its ability to withstand external pressure. It includes details like tester information, individual test data, average strength measurements, and the final pass/fail result.
Dye Penetration Test Results (ASTM F1929)
This section focuses on identifying potential contamination risks. It details the testing process and its outcome in relation to any discovered channels within the seal.
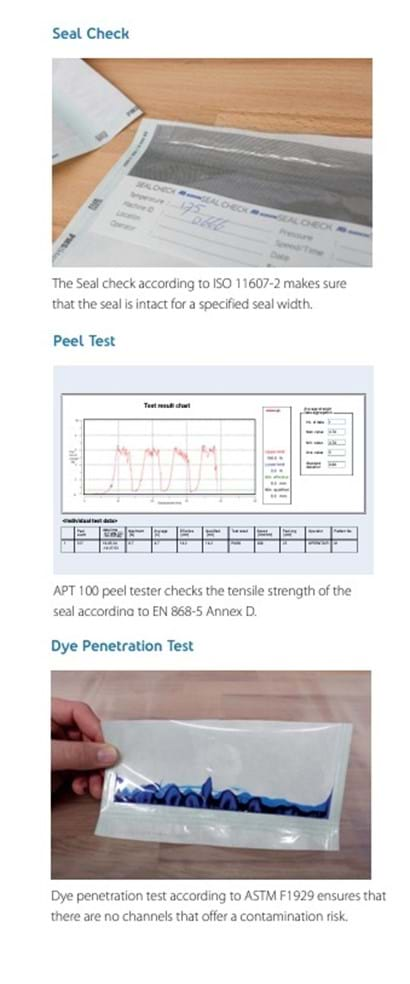
Audion Verification Instruments
Let's have a chat
Do you want to know what the Audionvac VMS 253 can offer for your company? Please feel free to contact us as we are looking forward to exploring together which packing solutions benefit you most
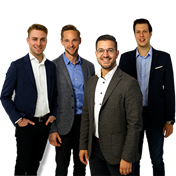
International Sales
Audion